Audi teste sa capacité à gérer les ressources en boucle
Le constructeur allemand a lancé le projet MaterialLoop qui fournit des indications précieuses sur la manière dont une économie circulaire peut être mise en pratique. Il s’agit notamment d’expérimenter la réutilisation de matériaux (acier, aluminium, verre et plastique) provenant de véhicules hors d’usage, mais aussi d’améliorer le potentiel de recyclabilité des prochaines générations de véhicules de la marque. Explications.
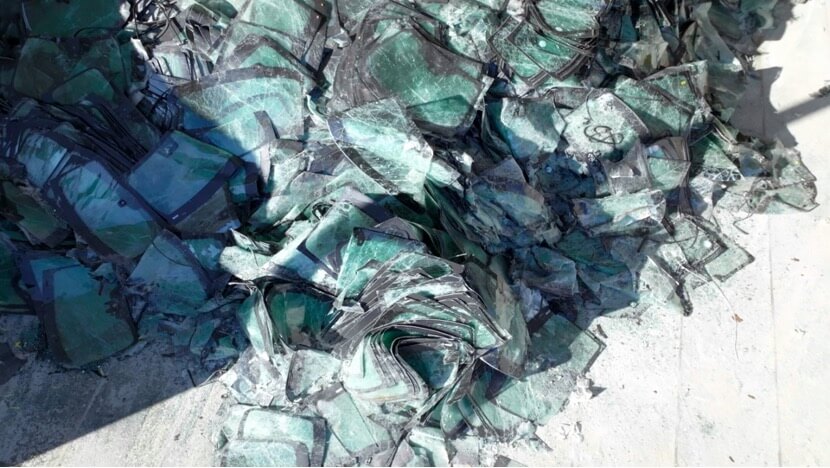
Dans le cadre du projet « MaterialLoop », lancé par Audi en octobre 2022 avec quinze partenaires des secteurs de l’industrie et de la recherche, le constructeur allemand a étudié la réutilisation des matériaux de post-consommation prélevés sur les véhicules hors d’usage (VHU) à destination de la production de nouvelles voitures. Le projet commun permet ainsi à Audi de développer ses connaissances sur les enjeux et les applications de la recyclabilité. Les parties intéressées se demandent par exemple quels matériaux présentent encore un potentiel, quels nouveaux procédés techniques doivent être développés et ce qui est d’ores et déjà réalisable aujourd’hui sur les plans économique et écologique. L’objectif est de « boucler » à l’avenir davantage de cycles de matériaux pour l’acier, l’aluminium, le plastique ou le verre dans l’industrie automobile et de donner une « seconde vie » aux ressources. L’idée a été testée en détails sur un panel d’une centaine de véhicules jusqu’à fin avril 2023.
Ainsi, dans le cadre de ce projet MaterialLoop, Audi souhaite utiliser une grande partie de l’acier recyclé pour produire jusqu’à 15 000 pièces intérieures de porte destinées à la gamme A4, à l’usine de presse d’Ingolstadt en Allemagne. Par exemple, le modèle Audi Q4 e-tron peut contenir jusqu’à 27 composants partiellement recyclés.
« Notre objectif est de récupérer autant de matériaux que possible à un haut niveau de qualité et de les réutiliser dans la production. Cela permettra d’économiser de précieuses matières premières et de réduire l’empreinte écologique des produits. Simultanément, l’accès direct aux matières secondaires peut contribuer à une sécurité d’approvisionnement accrue […] », explique Markus Duesmann, le patron d’Audi. Le démontage ciblé des différents composants a en effet permis de conserver des matériaux secondaires afin de les recycler. Les carrosseries restantes ont été broyées et triées en quatre groupes de matériaux : acier, aluminium, plastique et verre. La marque aux quatre anneaux a également défini et piloté le processus de recyclage ultérieur avec les partenaires du projet issus de l’industrie du recyclage, de la chaîne d’approvisionnement Audi et du monde universitaire, avec pour objectif de tester la réutilisation de ces matériaux dans la production de véhicules neufs.
Améliorer la capacité de recyclage des prochains véhicules
Désormais, MaterialLoop doit aider Audi pour la conception et la construction de futurs modèles afin d’en augmenter la recyclabilité. Ainsi, le programme « design for circularity » prévoit de dresser la sélection, la composition et la modularité des matériaux dès la fin de vie du véhicule afin de déterminer leur potentiel de réemploi.
« IL EST ESSENTIEL QUE L’UTILISATION DE MATÉRIAUX SECONDAIRES NE SOIT PAS EN CONTRADICTION AVEC DES EXIGENCES DE QUALITÉ ÉLEVÉES »
Dans le domaine de la réutilisation du verre, les granulés – récupérés à partir des vitres automobiles qui ne peuvent plus être réparées- sont fondus et transformés en un nouveau verre plat qui entre déjà dans la production de l’Audi Q4 e-tron. Le même procédé est appliqué pour les boucles de ceinture de la nouvelle Audi Q8 e-tron qui contiennent des déchets plastiques automobiles mélangés. « Dans ce cas comme dans tous les autres, il est essentiel que l’utilisation de matériaux secondaires ne soit pas en contradiction avec les exigences de qualité élevées », prévient le constructeur.
Miser sur le recyclage chimique des plastiques
Le recyclage des déchets plastiques mixtes pose néanmoins un défi majeur. Le constructeur utilise une technologie par pyrolyse mise au point avec l’Institut de technologie de Karlsruhe (KIT) en Allemagne. Le projet pilote intitulé « Recyclage chimique des plastiques en ingénierie automobile » vise à la création de systèmes circulaires intelligents pour les plastiques en complément du recyclage mécanique. Dans un premier temps, Audi entend tester la faisabilité technique du procédé et évaluer la méthode en termes d’économie et d’impacts environnementaux. Ce projet est mené par le groupe de réflexion « Industrial Resource Strategies » que le gouvernement de l’État du Bade-Wurtemberg, en collaboration avec l’industrie et soutenu par le milieu universitaire, a mis en place au KIT.
« Nous voulons établir des systèmes circulaires intelligents dans nos chaînes d’approvisionnement et utiliser efficacement les ressources. Le recyclage chimique a un grand potentiel pour cela : si les composants en plastique peuvent être produits à partir d’huile de pyrolyse au lieu de pétrole, il serait possible d’augmenter considérablement la proportion de composants fabriqués de manière durable dans les automobiles», explique Marco Philippi, directeur principal de la stratégie d’approvisionnement d’Audi.
Le constructeur fournit ainsi à l’institut des composants en plastique usés tels que des réservoirs de carburant, des pièces d’enjoliveurs et des grilles de radiateur, provenant
notamment de modèles en fin de parcours du réseau de distribution allemand. Ces composants sont alors transformés en huile de pyrolyse par recyclage chimique. L’intérêt est que qualité de cette huile obtenue est comparable à celle des produits dérivés du pétrole. Audi est l’un des premiers constructeurs automobiles à tester cette méthode de recyclage dans un projet pilote avec des plastiques issus de la production automobile.
Réduire les émissions de CO2 dans la chaîne de valeur
Par ailleurs, l’objectif du programme CO2 de l’entreprise est d’utiliser les ressources aussi efficacement que possible et de réduire les émissions carbone dans la chaîne de valeur en amont, en se concentrant sur les matériaux qui sont soit requis en grandes quantités, soit impliquant des processus de fabrication particulièrement énergivores.
Un exemple accompli, souligne le portail zegreenweb.com, est le programme « Aluminium Closed Loop » avec lequel Audi et ses fournisseurs ont réussi à récupérer les déchets d’aluminium et à les améliorer au niveau de la qualité des nouveaux produits, évitant ainsi au bilan environnemental près de 150 000 tonnes métriques de CO2 uniquement sur 2019. Les chutes liées à la production sont renvoyées au fournisseur, puis sont recyclées pour former des feuilles d’aluminium qu’Audi réutilise ensuite dans sa production. La boucle de recyclage est gérée depuis 2017 sur les sites d’Ingolstadt, Neckarsulm (Allemagne) et de Gyor (Hongrie), ainsi que sur le site Volkswagen de Bratislava (Slovaquie).
Afin d’augmenter progressivement la proportion de matériaux secondaires dans ses modèles, l’exemple le plus récent est l’utilisation du PET, un polymère plastique qui peut être séparé des autres matériaux avec lesquels il a pu être combiné. Pour le modèle A3, par exemple, trois housses de siège en textile sont disponibles avec un taux de matériaux recyclés allant jusqu’à 89 %. À l’avenir, toutes les housses de siège en textile dans toutes les gammes sont supposées être fabriquées à partir de matériaux recyclés.
Faurecia réinvente le siège automobile
Bien évidemment d’autres constructeurs et équipementiers se penchent sur la question stratégique du recyclage. On sait ainsi que lors du dernier salon de l’électronique CES à Las Vegas, Faurecia (société du groupe Forvia) a justement dévoilé une nouvelle façon de concevoir et fabriquer les sièges automobiles. Son alternative aux standards actuels est un siège modulaire, composé d’un nombre limité d’éléments en lieu et place d’un grand nombre de composants, conçus à partir de matériaux durables. Ces modules s’assemblent et se démontent facilement, permettant de renouveler les équipements du siège et d’y ajouter de nouvelles fonctionnalités tout au long de son existence, prolongeant ainsi sa durée de vie… tout en facilitant le recyclage.
Sur les 8,3 milliards de tonnes de plastique produits chaque année dans le monde, 6,3 milliards deviennent des déchets qui sont recyclés à seulement 9 %. L’immense majorité, soit 79 %, est en train de s’amonceler sur les sites d’enfouissement ou se répand dans la nature sous forme de détritus, déplore l’ONU. C’est dans ce contexte que Michelin propose de produire des pneus à partir de déchets plastiques recyclés. En effet, le fabricant leader mondial entend utiliser pour ses pneus, d’ici 2030, 40% de bouteilles de plastique recyclées et atteindre 100% en 2050. Le projet est ambitieux ; pour autant Michelin est la première entreprise à avoir produit et testé des fibres techniques destinées à être utilisées dans les pneumatiques.
Pour sa part, Stellantis va lancer une activité dédiée pour les véhicules hors d’usage d’ici la fin de l’année 2023 après avoir conclu un accord avec Galloo, son futur partenaire dans cette co-entreprise, spécialiste du recyclage de métaux. L’activité doit permettre à Stellantis d’atteindre les objectifs de son plan stratégique 2030, en « multipliant par 10 le chiffre d’affaires lié au recyclage, et par 4 celui des pièces détachées par rapport à 2021 », peut-on lire sur le site du constructeur.
Enfin, avec la montée en puissance des véhicules électriques en Europe et dans le monde, la production des métaux qui composent les batteries est devenue un enjeu majeur. Pour sécuriser l’approvisionnement, plusieurs projets d’extraction, de gigafactories ou de recyclage ont été annoncés en Europe (voir notre précédent article). Car dans cette chaîne de valeur, le raffinage est essentiellement réalisé en Chine, avec une concentration située entre 70% et 80% selon les métaux. Une dépendance que l’Union européenne souhaite enrayer avec un objectif de raffinage de 40% des métaux sur son territoire d’ici à 2040.
Toute l’actualité de Movin’On
dans votre boîte mail
Auteur
Partager
Tweets de @movinonconnect
Movin'On 2035 TODAY EP02 - Circular Economy & Competitivity
Movin’On 2035 TODAY EP01 – Fair Mobility for All https://x.com/i/broadcasts/1yNxagBrWZbGj
✨ THAT'S A WRAP!
Movin'On Summit 2024 has just concluded in Brussels!
More than 350 leaders and experts in sustainable mobility gathered to exchange ideas, collaborate, and share their vision for desirable and decarbonised mobility in Europe. Together, we explored ways to build…
🔴 Live from #MovinOnSummit2024
@AshaSumputh has just invited Denis Machuel, CEO at @AdeccoGroup and Florent Menegaux, President of the @Michelin Group & President of Movin'On
L’actualité de la mobilité durable
Découvrez les dernières tendances, des analyses thématiques et nos prochains rendez-vous